The Role of AI and Robotics in Enhancing or Threatening Workplace Safety
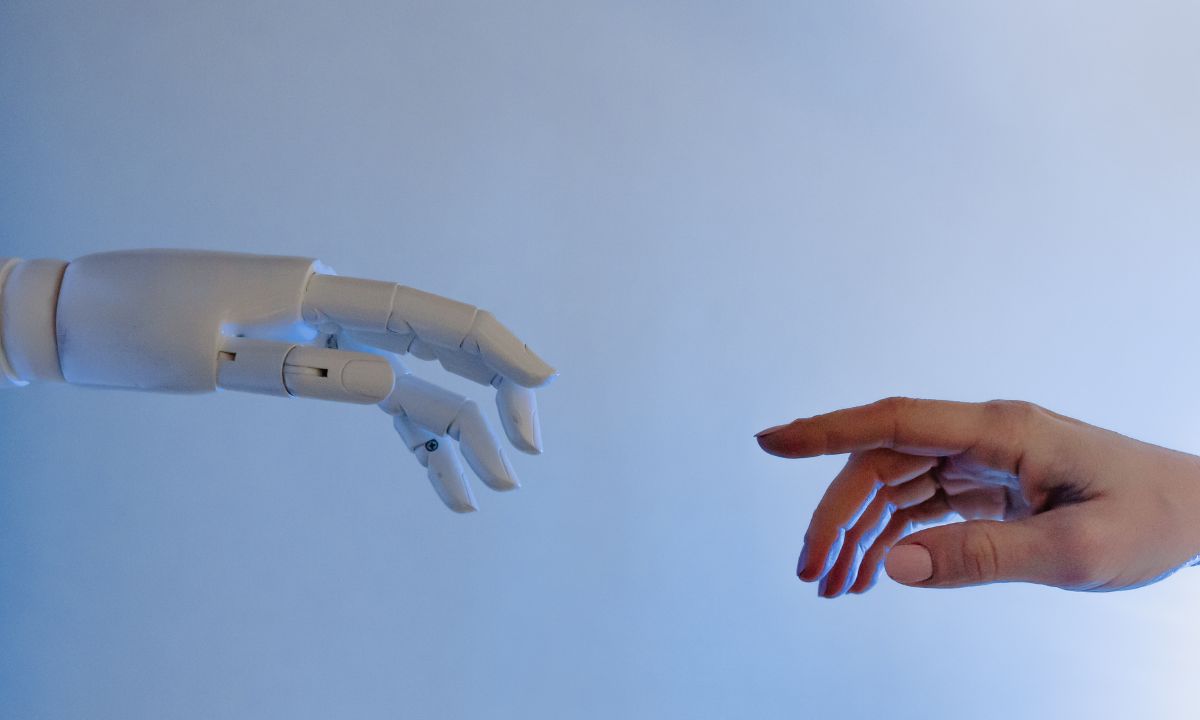
As businesses look to make operations smoother and safer, many are starting to look towards AI and robotics as the solution. These technologies have made massive leaps in both sophistication and prevalence in recent years, with over 68% of Australian businesses using some form of AI.
But, are AI and robotics a workplace safety miracle, or are they more trouble than they are worth?
The Benefits of AI and Robotics for Workplace Safety
There are a plethora of ways in which AI and robotics can be used to make things safer in the workplace, with varying applications to suit all sorts of businesses and industries.
AI as a Health and Safety Tool
Wearable tech is popular for monitoring worker wellbeing, with AI designed to track vitals such as heartbeat, temperature, and breathing, warning the wearer should they reach unsafe limits. As an example, for those working in extreme heat or with high physical exertion, such as tradies, such interventions can help to remind workers to take adequate breaks and reduce the risk of long-term health issues and complications.
AI can also be used to detect potential hazards by scanning the environment and letting workers know about issues and dangers such as spillages or equipment failures. Using this data, some AI programs can even create evacuation plans that take into account staffing numbers and locations.
Robotics Saving Workers
In areas where work may be too hazardous, some workplaces have invested in robots. This is not meant to replace human workers, but instead to safeguard them from harm, for example when working with hazardous materials, heavy weights, or perhaps extreme weather or temperature.
They can also be used in spaces where it may not be suitable for a human worker, for example in smaller, cramped spaces, or working at height.
Industry Examples of AI and Robotics in the Workplace
AI and robotics are already being used successfully in multiple industries and companies around the globe. Here are some of the top sectors already using the technology to help their workers.
Manufacturing and Logistics
There are a multitude of ways in which AI and robots can be used in the logistics and manufacturing industries, and so it stands to reason that this is where we see the most implementation of this kind of technology.
In manufacturing, AI can provide awareness of potential hazards, and machines such as robotic arms can be used for handling hazardous materials and dangerous machinery. In logistics, robots can be used to lift heavy loads safely and transport them efficiently, with AI being used to calculate safe load balancing.
However, one thing that these industries have in common is that the work undertaken is often repetitive and dull. This can lead human workers to become bored or complacent, increasing the risk of accident or injury. Using robots to do these incredibly menial and under-simulating jobs can remove that risk, or AI monitoring can help to keep workers alert and remind them should they start to lose focus.
Waste Management
Sifting through rubbish isn’t exactly most people’s description of a good time, and so in the waste management and recycling sector AI and robots can help to fulfill these tasks. Not only do they perform a role that is seen as undesirable, but they also protect workers from certain risks from dangerous materials that may be hiding within the waste being processed. AI also has a greater level of detection for certain materials, helping workers to be able to find and sort them to aid recycling efforts.
Construction
The construction industry is one of the world’s most dangerous occupations. By developing robots that can undertake the most dangerous tasks at a construction site, the risk to human workers can be minimised.
But, construction projects vary, and there isn’t a one-size-fits-all solution to protect workers by doing the most high-risk work for them. Instead, this is where AI comes in. It can monitor employee vitals to make sure they are working in safe conditions and not overexerting themselves or becoming too tired, and it can also scan the surroundings to alert workers and construction managers of potential dangers to prevent them before they happen.
Potential Risks and Downsides
It’s important to remember that AI and robots are not a magic wand for workplace health and safety. The technology is not immune to errors, and more time is needed to work out its full effectiveness.
For example, equipment or programs could malfunction, which could not only create a dangerous situation in and of itself but would remove the protections that workers had gotten used to while it is being fixed, which could also lead to further incidents. In the same vein, workers could get complacent or over-reliant on the technology, meaning that if it fails or needs to be turned off or removed for a while, they may have lost the necessary skills to be able to complete their work safely.
Although it is becoming more advanced, AI is definitely not human. So, programs that use AI to monitor employee well-being and productivity could potentially cause more harm than good as they are unaware of the physical and mental limitations of workers.
Generative AI is thought to be one of the top ways for companies to be able to boost employee productivity, but this is primarily a factor within highly skilled or white-collar occupations. When it comes to manual labour or work involving a large amount of movement or physical activity, AI can actually end up being more harmful than helpful. As an example, we can look at the AI productivity monitoring of Amazon back in 2019. The programs would consistently see workers doing an adequate job as underperforming based on their metrics, leading employees to push themselves to unsafe levels and some even facing dismissal due to the feedback from the AI productivity system.
There is also a risk when it comes to worker morale and sentiment. Employees may feel that they are being replaced, which could cause unrest or staffing problems as they seek employment elsewhere. However, studies have found that in instances where AI and robotics have been introduced for the purpose of increasing workplace safety, employees are much more welcome and accepting of the change. Therefore, businesses implementing these technologies should make sure that relevant information and clarification are given to their workers to allow for a seamless integration.
Future Trends and Considerations
As the technology continues to develop, we are likely to see more implementations of robotics and AI in the workplace. As AI starts to learn more about the intricacies of certain industries, it can better be used to predict and detect hazards with a lower margin of error than human managers and officials. It can also be used to analyze various data sets much faster than a human could to be able to assess and provide strategies for health and safety frameworks and emergency responses.
Robotics are expected to become more advanced, able to complete more tasks and be increasingly tailored to certain dangerous tasks, such as working in confined spaces. Reliability will also improve, meaning that workers won’t have to cope with as many mechanical failures that could hamper production.
At the same time, governments and agencies need to keep on top of any new changes to make sure they are safe and of benefit to workers. Although there is no concrete legislation in place, should these technologies prove to be a significant benefit or danger, we expect this could change as they become more prevalent.
Overall, it is far too early to say whether robotics and AI will be a help or a hindrance when it comes to workplace safety, but the best way you can learn is to stay on top of changes in your particular industry for better or worse.
If it's time to talk, we're here to help. Get free advice direct from our solicitors today.
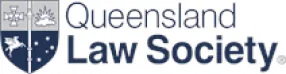
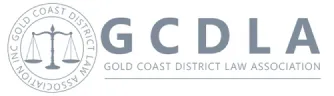
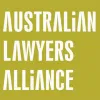
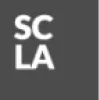